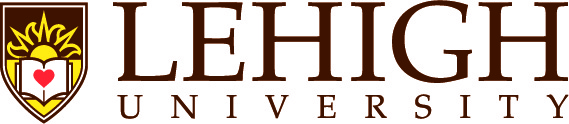
In this episode of Lehigh University’s College of Business IlLUminate podcast, we are speaking with Phillip Coles about how disruptions in the supply chain will affect this holiday season.
Phil is a professor of practice in the Decision and Technology Analytics Department at Lehigh Business. He has an MBA from Lehigh and an MS from Cornell. And Phil has over 30 years of industry experience, including being vice president of strategic management at a multi-million dollar produce company.
He spoke with Rob Gerth, director of marketing and communication for the College of Business. Listen to the podcast here and subscribe and download Lehigh Business on Apple Podcasts or wherever you get your podcasts.
Below is an edited excerpt from that conversation. Read the complete podcast transcript.
Rob Gerth: Right now, when we go to the store, we're seeing less product and we're seeing it selling at higher prices. We're talking about everything from Halloween costumes to artificial Christmas trees to toys. And the story on the news channels are all about the toys, but it's not just toys, right?
Phil Coles: No, it's not just toys. There's a lot of different things that are being affected throughout all the different supply chains.
Gerth: But there is supply and there is demand for these things, even for the toys. They've made the toys. That's not the problem. So how does the supply chain part of this figure into it?
Coles: Well, it depends on what kind of industry you're talking about. The toys? Yes, they've been made. 85% of toys come from China, and they're sitting in warehouses in China. They're sitting in ships off the coast of California. They're sitting in warehouses right outside of the ports that are in California. Some of them were being shipped to other ports around the country because they can't take them through the Port of Los Angeles. There's a general problem with ports on the West Coast just because of the volume that's trying to come through there. There’re also other issues in supply chain, too, because you've got the operations standpoint. For example, automobile sales are down significantly because of chip shortages. So with the toys, it's a shipping issue. When you're talking about automobiles, it's actually a production issue because of chip shortages.
Gerth: When did the problem first show? When did people start panicking, I guess, about the holiday season in particular? When did people start figuring that out that, "Hey, it looks like there's going to be a problem." How long have we known about this?
Coles: Well, the general public hasn't known about it for that long, but the people in the industry know. And this is a common problem. These are tradeoffs that we make in our supply chains. So, one the issues a lot of people conflate, and for whatever reason, lean manufacturing with globalization, and they are actually the opposite of each other. And with lean manufacturing, you're trying to reduce inventory, particularly in process inventory. When you think about a long supply chain, you got something coming from, say, Shanghai to the United States. It's a very long supply chain. You've got a lot of inventory that's on the water. So, we think about it as shipping, but it's also a way to hold inventory. It's not intentional, but there's inventory that's on the ships that are coming over.
People in business, they make a trade off. There's truly no right answer. Everything is about tradeoffs. What risks are we willing to take on for whatever possible gains that we can get from it? So, if you can get products for less price or a better quality from somewhere far away, you say, "Okay, the risks of that long supply chain are worth it." So most of the time, it works out really well. But when you get these shocks to the supply chain and you've got a lot more risk with a long supply chain because a lot of things can happen, it can cause these disruptions. And we always know that there's the possibility. It's just that it rarely happens.
We need to be prepared for when these things happen. And this was really something that kind of came out of left field. Nobody could anticipate this. But it's always difficult for the Christmas season because you got to order almost a year in advance. And it's hard to have a really good crystal ball and know what's going to happen within the next year.
Gerth: What portion of the supply chain problem that we have now can we blame on the pandemic or is it to be blamed on just how the system is?
Coles: You always have the weak players go out whenever you've got some kind of a shock, whether it's low prices, shortage issues or what have you. The better players are making more money in good times than the weaker players. But then when prices go down or there's not as many sales or whatever it's happening, that's when you're going to see the weak players go out. And that's also where you get the people that have the short-term horizons. So, we talked about sometimes companies making or the management of companies making poor decisions. Well, sometimes they make that decision, they say, "I can save a lot of money by not having fire insurance on my company." And you do really great because you don't have the insurance, until you have a fire, then you wish you'd had the insurance.
Any kind of risk management, that's what insurance is. It's risk management, is part of doing that. So, if you're flying without doing risk management, you're taking on a lot of risk. So, the simplest thing to do that everybody thinks of and everybody thinks is the issue, is to have some extra inventory, but it's much more important to have a flexible, responsive supply chain and do risk management where you have alternative suppliers and you have alternative products that you can use to replace them. I like to use the example of when there was a copper shortage in the 1970s and you couldn't get enough wire, copper wire. They went to aluminum wire.
The companies that are having issues-- and I don't want to make it sound like this would have been easy. Nobody knew there was going to be a pandemic and then all the responses that happened. This is very difficult.
Gerth: Can we save Christmas, Phil?
Coles: This is nothing new, just to put it in perspective. In 1983, the Cabbage Patch Kids dolls, remember those? In 1982, we were mired in a recession. Nobody imagined what kind of a recovery we would have. In 1983, it came roaring back. Again, long supply chains. They thought, "Okay, we've got an order for Christmas of 1983, and it's early 1983, almost a year ahead of time." And they thought the economy was going to be bad. They didn't order enough.
And there were all these conspiracy theories out there that they thought, "Okay, we have a shortage of Cabbage Patch Kid dolls because they want the prices to be higher." And they probably just screwed up. They didn't know. Their crystal ball wasn't that good. So I bring that up for some perspective. So, if we compare what's happening in the supply chains to perfect, it's horrible. You compare anything to perfect and it's horrible.
But if we compare how we've done in the past and take into consideration these tremendous shocks that our supply chains have taken, it's amazing that we have anything. It's really a tribute to how well they're doing. So we're going to have stuff for Christmas. You might not be able to get the exact thing that you want. You might not be able to get it for the price that you want. You're going to be able to get something. And some people may have to be a little creative.
And I remember one of the things people were doing, they had little, tiny Cabbage Patch dolls that were like just the face and a flower and things like that. They would give it to their kids and with the promise of getting the real thing after Christmas. In January, February, they all started showing up. But yeah, we'll be okay, I think. It'll be a few disappointed people. But overall, I think we'll survive.